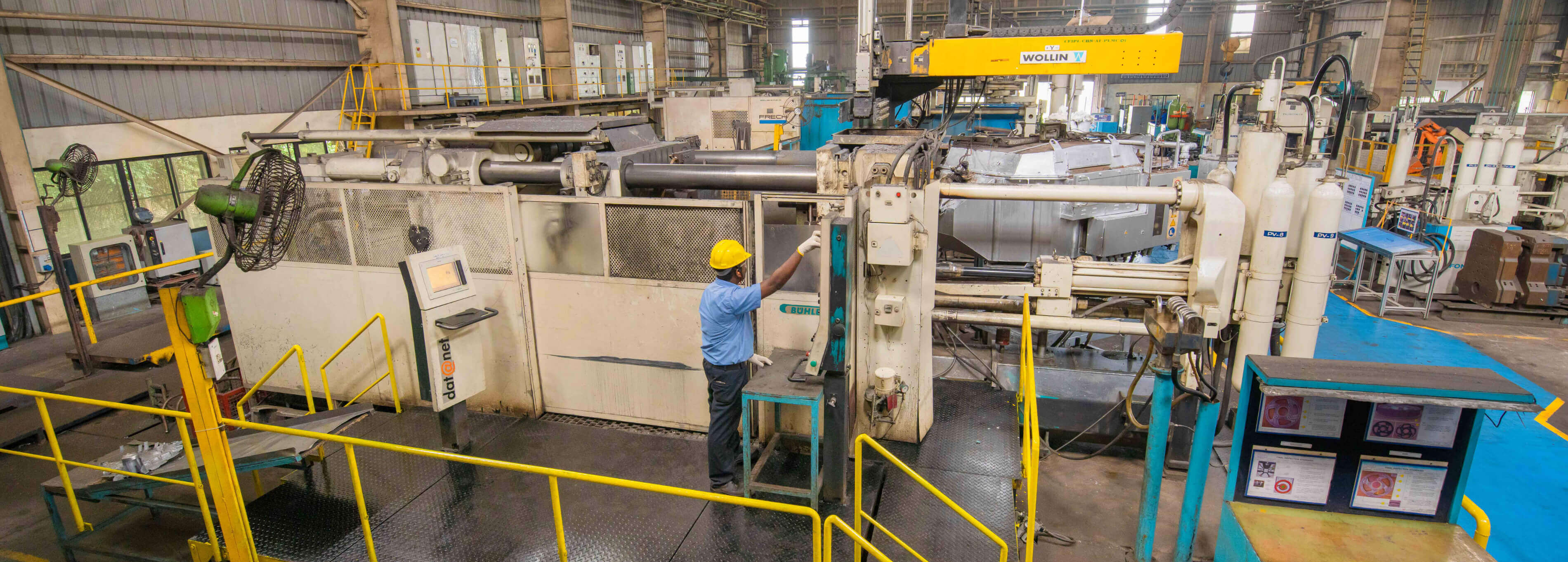
HPDC Facility
The division has installed 7 high pressure die casting Buhler machines ranging from 250T to 1600T and each machine has a holding furnace and Jet cooling facilities. The facility has provision for partial squeeze technology and vacuum die casting. All the process parameters are being controlled and recorded through real time controllers. The technology used ensures high volume along with the dimensional accuracy and surface finish which require minimum machining, thereby offering cost advantage to the customers.
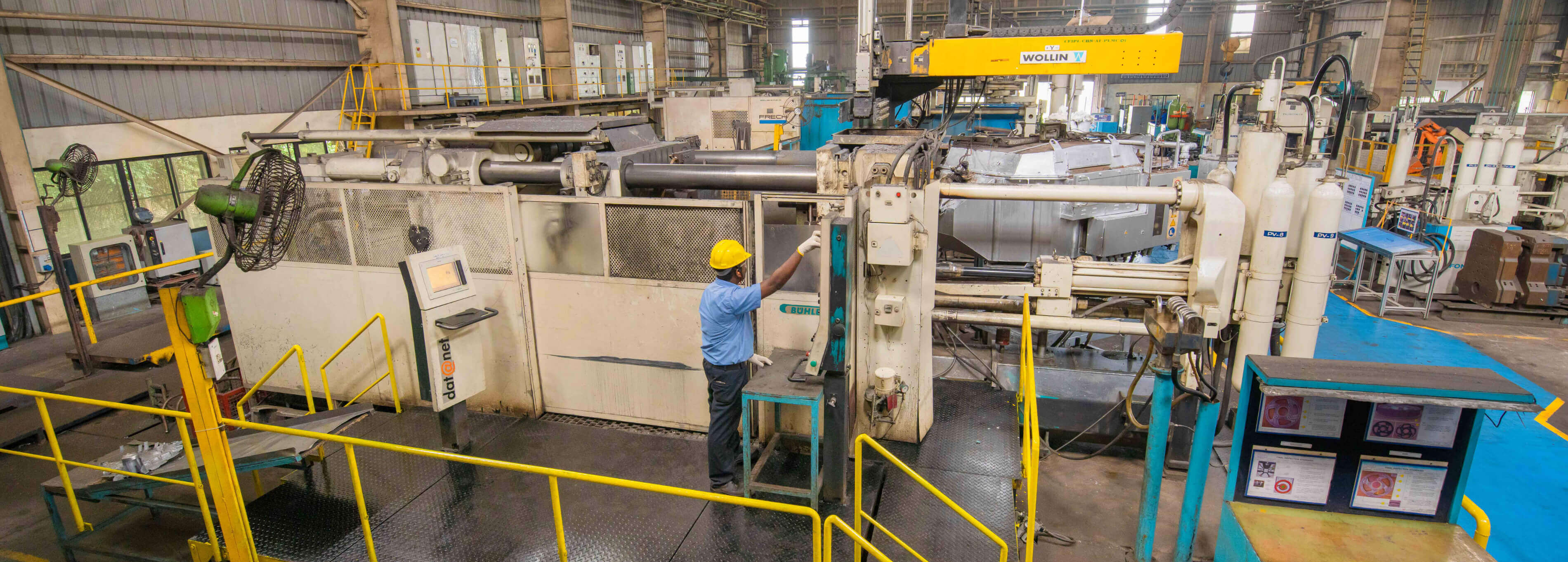
HPDC Facility
The division has installed 7 high pressure die casting Buhler machines ranging from 250T to 1600T and each machine has a holding furnace and Jet cooling facilities. The facility has provision for partial squeeze technology and vacuum die casting. All the process parameters are being controlled and recorded through real time controllers. The technology used ensures high volume along with the dimensional accuracy and surface finish which require minimum machining, thereby offering cost advantage to the customers.
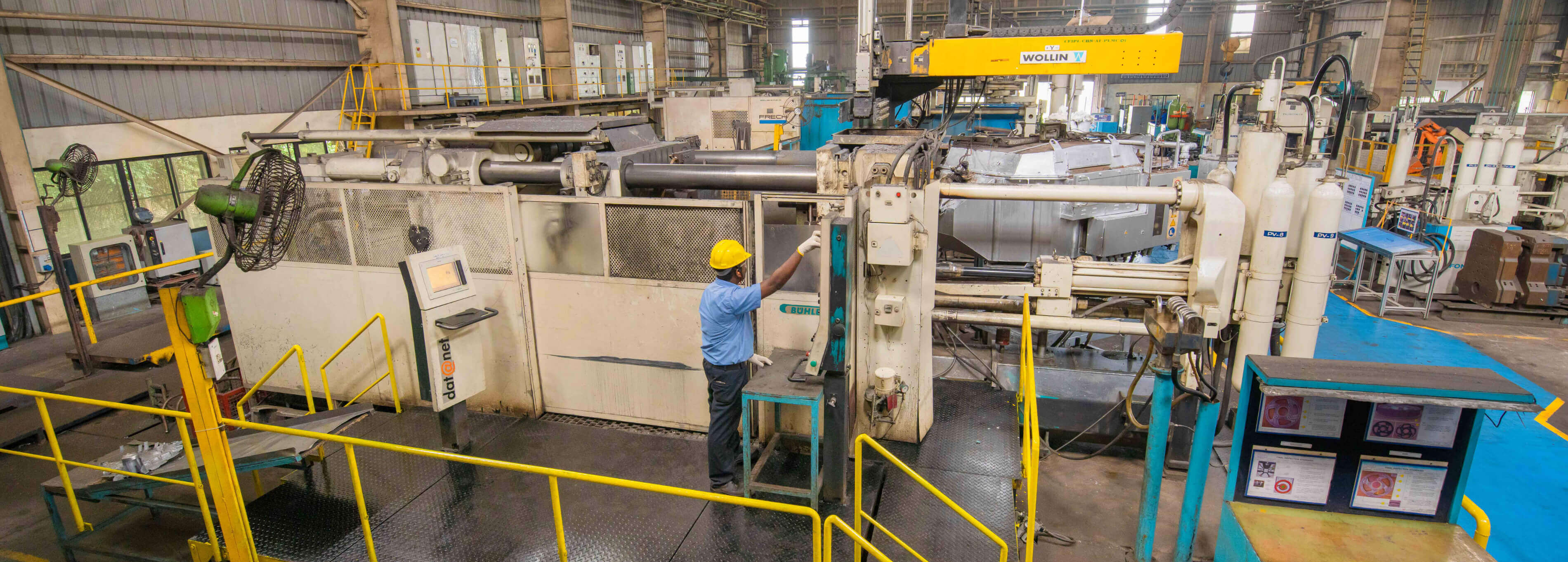
HPDC Facility
The division has installed 7 high pressure die casting Buhler machines ranging from 250T to 1600T and each machine has a holding furnace and Jet cooling facilities. The facility has provision for partial squeeze technology and vacuum die casting. All the process parameters are being controlled and recorded through real time controllers. The technology used ensures high volume along with the dimensional accuracy and surface finish which require minimum machining, thereby offering cost advantage to the customers.
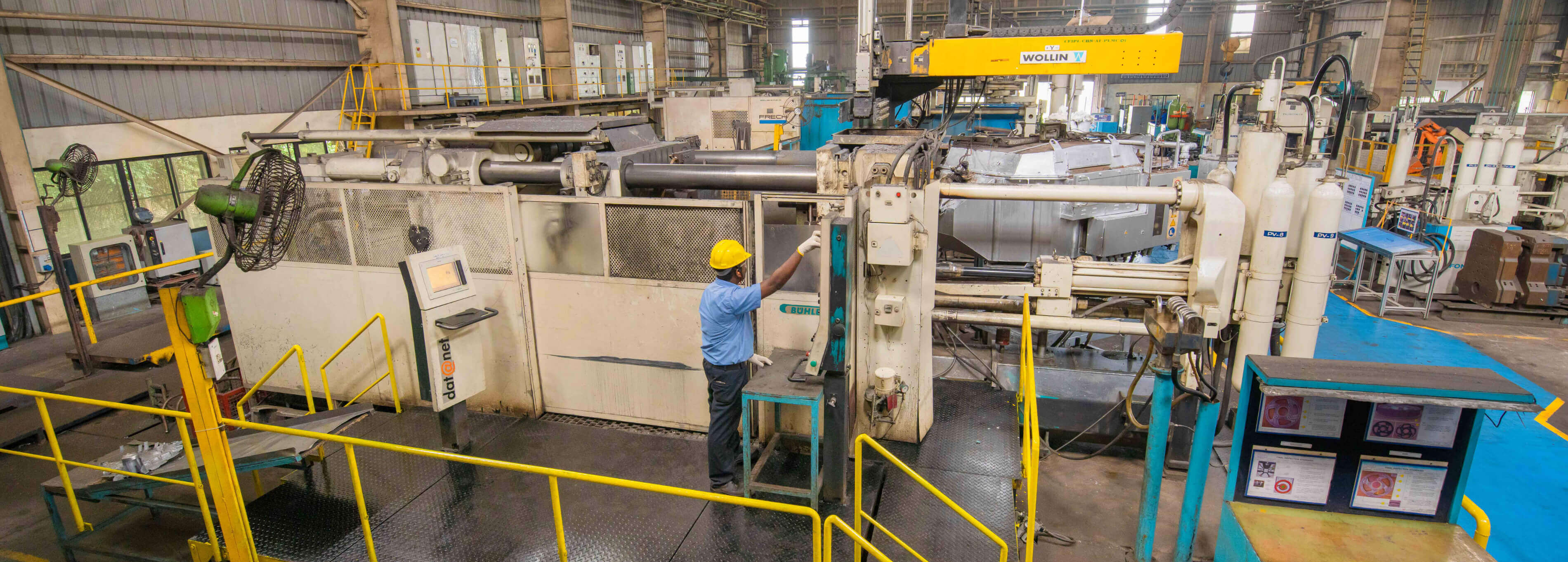
HPDC Facility
The division has installed 7 high pressure die casting Buhler machines ranging from 250T to 1600T and each machine has a holding furnace and Jet cooling facilities. The facility has provision for partial squeeze technology and vacuum die casting. All the process parameters are being controlled and recorded through real time controllers. The technology used ensures high volume along with the dimensional accuracy and surface finish which require minimum machining, thereby offering cost advantage to the customers.